Why Are There Bubbles or Cracking on my Air Cured Project?
DO NOT APPLY AIR CURE CERAKOTE TOO THICK
SOLVENT POP
Cause
Applying Cerakote too heavy may result in solvent pop or spraying in an environment with excessive humidity and heat can also contribute to blistering. Metallic colors are going to be more prone to this issue.
Effect
Solvent Pop happens when the outermost layer of the coating hardens before all the solvents have gassed off or evaporated. This forces gasses through the top layer of the finish and creates solvent pop or a blistering like effect.
If you have solvent pop, you will usually notice it within about an hour after application. Solvent pop looks like little bubbles under the coating or blistering. To fix this, you will need to re-sandblast parts, taking off the existing finish completely using either Aluminum Oxide or Garnet Sand #100 grit. When part is ready to be re-finished be cautious to not apply the new coat too heavy. Refer to the Application Guide that is specific to the product you are using for best results.
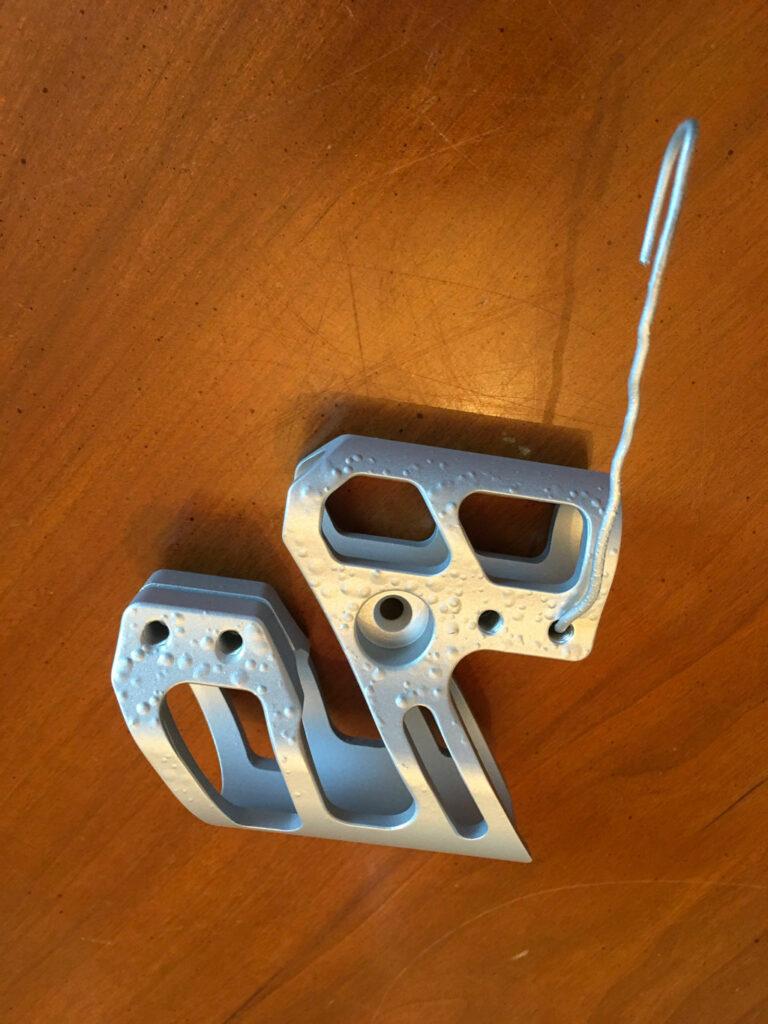
FLAKING OR DELAMINATION
Cause
Flaking or delamination is usually caused from surface contamination, prior to application, i.e. oil, grease, dirt, or excessive moisture. This can also occur if Cerakote is applied to thin, pushed passed its thermal stability or a poorly sand blasted profile. Cerakote needs a proper mechanical profile and film thickness for optimal performance.
Effect
Flaking or delamination is when the coating separates its self from the substrate.
Flaking of Cerakote will usually happen when exposed to high temperatures or operating temperatures. To fix this, you will need to re-sandblast parts, taking off the existing finish completely using either Aluminum Oxide or Garnet Sand #100 grit. When part is ready to be re-finished be cautious to not apply the new coat too heavy. Refer to the Application Guide that is specific to the product you are using for best results.
We suggest applying Cerakote C-Series and Glacier Series at 30 PSI. Glacier Series should only need one wet coat to achieve the l mil thickness recommended. Certain C Series products may take 2 or 3 coats to achieve their recommended film thickness. Be sure to check the Application Guides for specific information.