COLOR & APPLICATION OPTIONS
Cerakote
Cerakote offers over 200 unique and popular colors, and can be applied to all ferrous and non-ferrous metals, plastics, composites and many other substrates making it a universal coating as an anodizing alternative.
Anodizing
Due to the chemicals used in the process, anodizing offers a very limited color selection and can only be used on aluminum and titanium surfaces.
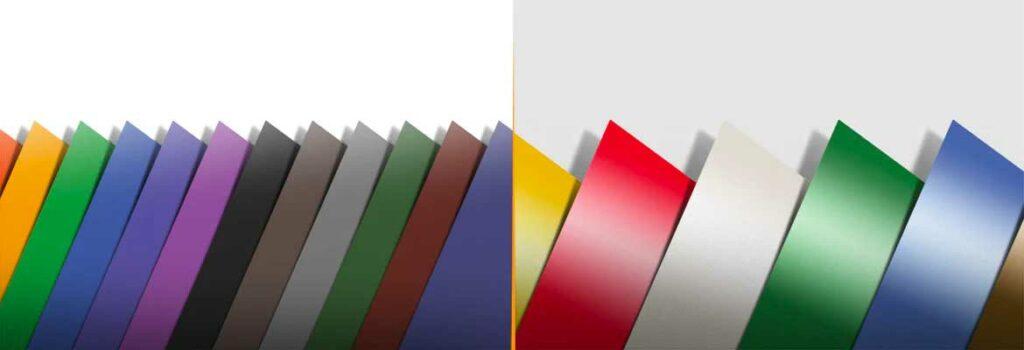
COLOR CONSISTENCY
Cerakote
All Cerakote colors are held to a color consistency standard of a Delta E of 1 or less. Typically, the human eye can only see color variance differences greater than a Delta E of 2 or more, making Cerakote the perfect anodizing substitution for high volume finishes.
Anodizing
Color consistency is known to vary widely from part to part and batch to batch due to chemical variations and subtle differences in the substrate that cannot be controlled.
IMPACT ON ALUMINUM ALLOYS
Cerakote
Cerakote does NOT detrimentally affect the fatigue properties of aluminum alloys.
Anodizing
The anodizing proceed creates a brittle and porous oxide layer and tensile residual stress, which detrimentally affects the fatigue properties of aluminum alloys. This fatigue has been widely reported and documented.
ENVIRONMENTAL IMPACT
Cerakote
Cerakote does not contain any heavy metals and is VOC exempt in all 50 states. Cerakote is a REACH, ROHS, and prop 65 compliant coating.
Anodizing
The chromic acid anodizing process releases hexavalent chromium, a powerful carcinogen, into the environment. As a result, the use of hexavalent chromium is becoming increasingly restricted by regulations.