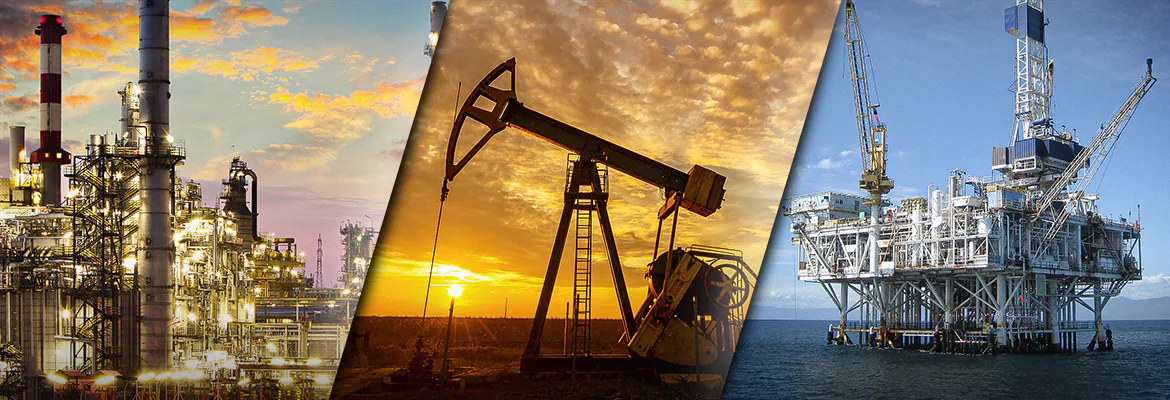
Cerakote ceramic coatings increases the longevity of parts by adding the industries best corrosion protection in an ultra-durable thin film coating. While other coatings claim big corrosion numbers, they simply don’t deliver on the parts that matter most.
Tight tolerance parts such as threads and valves are generally left uncoated due to the tolerance limitations of thick paints, powder coatings and plasma spray. This leaves the most critical areas of your operation exposed and unprotected. Not only does Cerakote have the industry’s leading corrosion protection, it can also be applied to the entire part (external and internal without the need for expensive masking), including the most difficult threads, valves, and impellers.
CERAKOTE IS KNOWN FOR:
- Unmatched corrosion protection- at 1 mil thickness our coatings surpass 4,000 hrs. of salt spray corrosion testing (ASTM B117) without failure.
- Excellent chemical protection – ideal for exposure to acids, alkaline solutions, drilling fluid, crude oils and byproducts, hydraulic fluids and more.
- Excellent abrasion resistance – handles high cycling, high wear environments. Rates 9H hardness and over 5,000 cycles per mil of abrasion resistance (ASTM D4060).
- Flexibility – Cerakote’s thin film design allows the coating to flex with the substrate. Great for thermal expansion and high vibratory environments.
- No masking required – Save time and money by eliminating costly masking during the coating process.
- Tight tolerance applications – excellent for use on threads, fasteners, values, pumps, and internals where paint and powder coating cannot be applied.
- High temperature applications – Coatings formulated to withstand temperatures up to 1,800° F, including thermal shock resistance, with no adverse effects.
- Superior low coefficient of friction – CoF of 0.11 that exceeds current market PTFE coatings.
Companies around the world use Cerakote for its industry leading chemical resistance, corrosion protection, durability, and tight tolerance finishes. Cerakote is applied to 100% of your part without any masking, which provides you with industry leading protection and durability without exception.
This testimony is from one of our customers in the Permian Basin that tested our products in the field and made the switch to Cerakote due to the radical increase in uptime and performance:
We began using Cerakote approximately two years ago. In the past, we have used epoxy coating to protect our steel & ductile iron parts. Most of the failure occurred in the threads which could not be coated. By using Cerakote, which allows us to coat threads, we have increased the life span of our connections. What was being changed every two to four months is now lasting over eighteen months. We are in the process of changing epoxy coated threaded fittings to Cerakote, as the steel fittings wear out and are replaced. — Chris Vestal (Production Supervisor; Layline Energy)
Common Coatings and Pre-treatments that Cerakote replaces:
- All paints
- Anodizing
- Iron Phosphate
- Zinc Phosphate
- Epoxy Primers
- Chromate
- Xylan®
- Powder Coating
- Fusion Bonded Epoxy
- Nickel Platingv
- Salt Bath Nitriding
- Galvanizing
- PTFE
Substrates Cerakote can be applied to:
- Aluminum – All grades
- Mild Steel
- Stainless Steel – All grades
- Inconel – All grades
- Superalloy
- Ductile Iron or Cast Iron
- Titanium
- Magnesium
Whether it’s for downhole tooling, flanges, valves, or threaded areas, Cerakote is the solution for your corrosion and durability problems.
Cerakote is dedicated to manufacturing the highest quality performance products for our customers. All our products are manufactured, produced, and shipped right here in the USA. We know the bottom-line matters. If it matters to you, Finish Strong™ with Cerakote.
HOW DO I GET STARTED WITH CERAKOTE?
Manufacturers, owners and operators, please contact us to discuss a complimentary demonstration of Cerakote on your equipment. Cerakote is available in over 85 countries and can be economically integrated into your current finishing process or outsourced to one of our factory trained Certified Applicators around the world.
Email us at [email protected] to find out more!